Placing Custom-made Medical Devices on the EU market
Placing Custom-made Medical Devices on the EU market
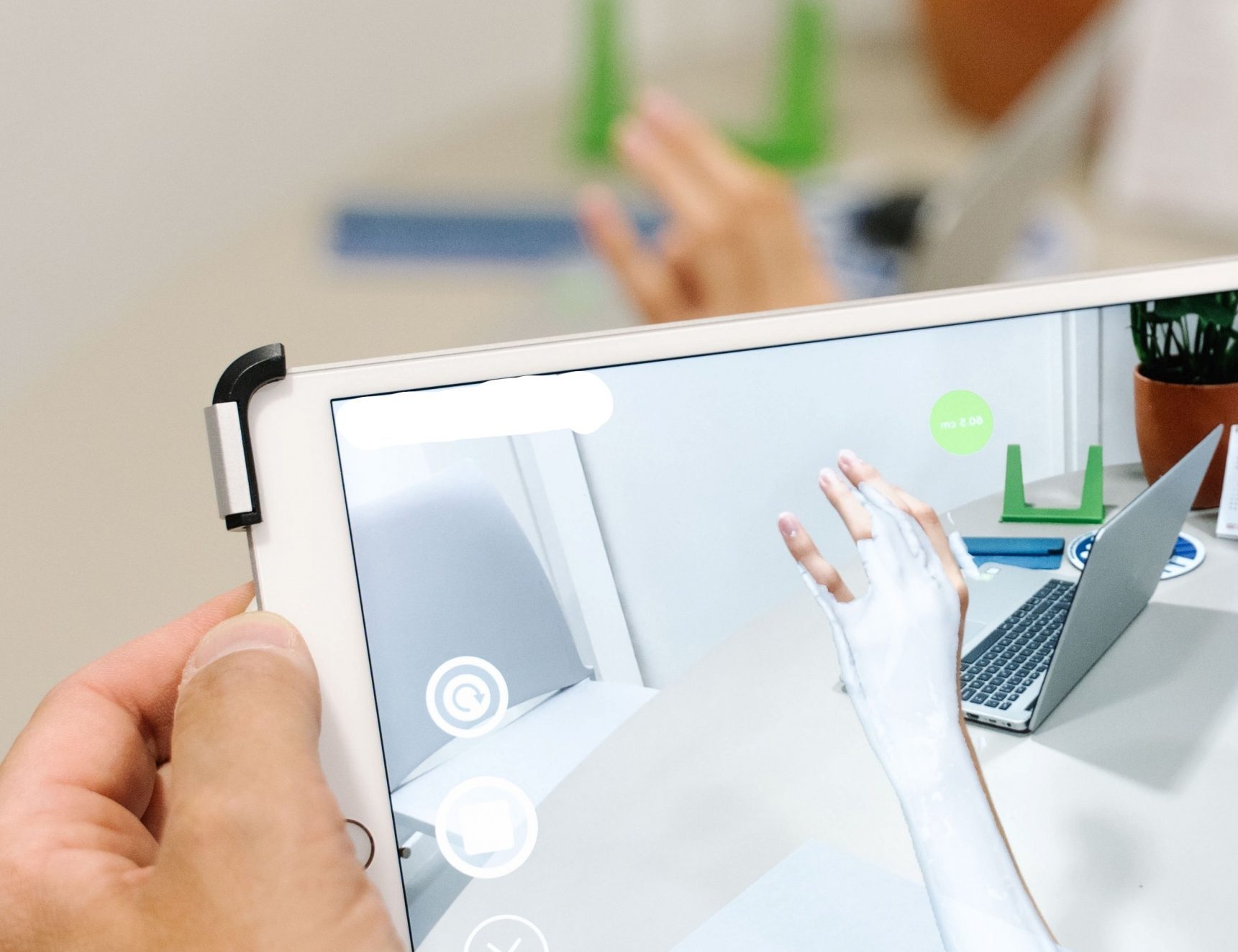
Amy Eikelenboom
Co-founder of NAALA
Published on 25 September 2021
Following our recent blogs concerning special product categories that are subject to specific European Medical Device Regulation (hereinafter: “EU MDR”) requirements, the custom-made medical devices (hereinafter: “CMDs”) shall not be forgotten. This blog details the specific rules CMD’s must comply to. But what are CMDs?
CMDs are defined as devices with the following characteristics:
- Specifically made in accordance with a written prescription of any person authorized by national law by virtue of that person’s professional qualification (health care professionals for example); which gives
- Specific design characteristics provided under that person’s responsibility; and
- is intended for the sole use of a particular patient exclusively to meet their individual conditions and needs.
Examples of CMDs include:
- A dental crown manufactured according specific design characteristics stated in a written prescription provided by a dentist to meet the individual condition of a patient.
- A prothesis made in accordance with a written prescription, where the practitioner provides patient specific design characteristics necessary for the manufacturing of the device.
There are other customizable device types that are not considered to be CMDs. These are the following two categories:
- Adaptable medical devices. These devices are mass-produced and must be adapted, adjusted, assembled or shaped at the point of care to suit an individual.
Examples of these adaptable medical devices are patient fitted wheelchairs, hearing aids and orthotic braces.
- Patient-matched devices. These devices do match patient specific anatomy but use a predefined range and an anatomic reference (e.g. following from patients images) to scale the devices specific to the patient concerned. These devices are still produced in batches. These devices are produced under the sole responsibility of the manufacturer and do not require a prescription, as is the case with CMDs.
An example of such a device are 3D printed plates, printed based on a template model and DICOM files/images of the patient.
In terms of EU MDR applicability, yes there are.
Broadly speaking the EU MDR makes a distinction between implantable CMDs that classify as class III[1] medical device and all other CMDs. The type of CMDs determines the conformity procedure to follow.
Manufacturers of Class III implantable CMDs are subject to a conformity assessment based on a quality management system[2] or may choose to apply a conformity assessment based on production quality assurance[3].
All other CMDs shall follow a conformity procedure specific for CMDs[4]. In the remaining of this blog, we will focus on the conformity procedure to be followed by these ‘other’ CMDs.
[1] In this blog we do not go into the classification of implantable medical devices. The classification rules of Annex VIII to the EU MDR might be useful in determining the classification. If additional clarification is required, do not hesitate to contact us.
[2] as specified in Chapter I of Annex IX
[3] as specified in Part A of Annex XI
[4] Annex XIII
Different form other medical devices, CMDs do not require the following:
- CE marking;
- The engagement of a notified body before making a custom-made device available for the medical practitioner and patient;
- UDI registration and labelling requirements;
- Registration of the person responsible for regulatory compliance (PRRC) in EUDAMED;
- A Summary of Safety and Clinical Performance (SSCP).
CMD manufacturers must meet nearly all EU MDR requirements. This includes the following obligations:
- establishment, documentation, implementation, maintaining, updating, and continually improving a quality management system (hereinafter: “QMS”);
- implementation of a post-market surveillance system
- demonstration of compliance to general safety and performance requirements, or, where applicable, indicating which general safety and performance requirements have not been fully met, together with the ground;
- providing a post-market surveillance report of Periodic Safety Update Report (PSUR), dependent on the risk classification.
Luckily, they do not.
Obligations for risk management, post-market surveillance and clinical evaluation life cycle processes specifically may be applied to groups of devices with the same intended purpose, materials used, process utilized, same principal design etc. Not to each individual CMD.
Additionally, a QMS can be implemented in such a way that it ensures the quality of all products manufactured in accordance with this QMS.
By following the applicable conformity assessment procedure, manufacturers of CMDs must have the following in place[1]:
- Drawing up a statement that contains all of the following information:
- The name and address of the manufacturer, and of all manufacturing sites,
- If applicable, the name and address of the authorized representative,
- Data allowing the identification of the device in question. CMDs are, however, not required to have an UDI.
- The name of the person who made out the prescription and who is authorized by national law by virtue of their professional qualifications to do so, and where applicable, the name of the health institution concerned
- The specific characteristics of the product as indicated by the prescription;
- A statement that the device in question conforms to the general safety and performance requirements set out in Annex I and, where applicable, indicating which general safety and performance requirements have not been fully met, together with the ground;
- Where applicable, an indication that the device contains or incorporates a medicinal substance, including a human blood or plasma derivative, or tissue or cells of human origin, or of animal origin;
- Documentation indication the manufacturing site(s) and allowing an understanding of the design, manufacture and performance of the device, including expected performance, so as to allow assessment of conformity with the requirements of this Regulation. Full Technical Documentation required for other medical devices do not apply to CMDs;
- Take measures to ensure that the manufacturing process produces devices which are manufactured in accordance with the beforementioned documentation;
- The statement referred to in section 1 shall be kept for at least 10 years after the device has been placed on the market and 15 years in case of implantable devices. This information must be kept at the disposal of competent authorities for the before indicated periods in case a manufacturer, or its authorized representative, goes bankrupt or ceases its business activity prior to the end of that period.
- Experiences gained in the post-production phase shall be reviewed and documented, including from Post-Market Clinical Follow-up[2] as referred to in Part B of Annex XIV, and implement appropriate means to apply any necessary corrective action. In that context, it shall report to the competent authorities[3] any serious incidents or field safety corrective actions or both as soon as it learns of them.
[1] As required by Annex XIII to the EU MDR.
[2] Post-Market Clinical Follow-up as referred to in Part B of Annex XI
[3] As required by Article 87(1)
Class III implantable CMDs are subject to a conformity assessment based on a quality management system[1] or may choose to apply a conformity assessment based on production quality assurance[2].
Both conformity assessments can be perceived as the ‘common conformity assessments’ to follow. This includes the involvement of a notified body and the provision of access to the technical documentation. More detail can be found in the beforementioned annexes.
[1] as specified in Chapter I of Annex IX
[2] as specified in Part A of Annex XI
Are you the manufacturer of CMDs and in need of support in EU MDR compliance? Please feel free to reach out.
Please note that all details and listings do not claim to be complete, are without guarantee and are for information purposes only. Changes in legal or regulatory requirements may occur at short notice, which we cannot reflect on a daily basis.
Other articles you may be interested in:
Liked the article? Maybe others will too. Feel free to share!